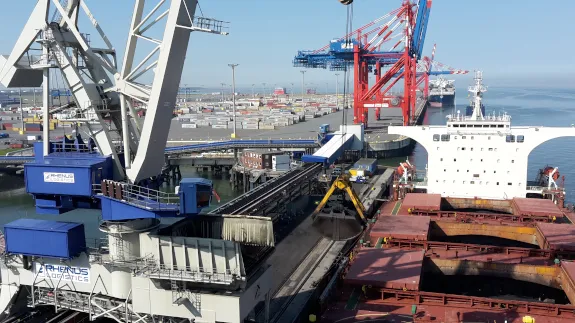
CASAR Superplast10 Mix was introduced and delivered to its first customer three years ago. At that time, the internal tests under laboratory conditions had just been completed and the rope started work on its first industrial and overhead cranes. In the meantime, the CASAR Superplast10 Mix had proved its versatility and was used in other applications.
The best example of this is the Rhenus Bulk Terminal Wilhelmshaven (formerly Niedersachsenbrücke) or BTW for short. There are Ø 42 mm Superplast10 Mix ropes in use on both the four fall double jib level luffing cranes. These have a load capacity of 63 t with an offset of 44 m; the gripper size is 44 m³. Together with the 38 t ship unloader overhead gantry crane, ships up to 250,000 t in size can be unloaded at a total unloading rate of 4,000 t/h. Cranes and grabs are one of the largest construction classes that the manufacturers of both trades can deliver.
As the name suggests, four ropes in total are used, two holding ropes (outside) and two closing ropes (inside). With this configuration, the grab does not twist under load, as both rope types are designed right handed and left handed.
The two holding ropes are connected to the grabber by rope sockets supplied by the customer. The closing ropes are also fastened with rope sockets to the gripping ropes inside. The connection with the rope socket ensures that the short strand length in the gripper can be changed quickly and easily.
The high number of bending cycles on relatively small pulleys combined with the abrasive action of the bulk material ensures that this short rope zone fails much earlier than the rest of the rope length and therefore must be changed much earlier.
When connecting the closing and gripping ropes, ensure that the left-hand closing rope is connected to the left-hand gripping rope and the right-hand closing rope is connected to the right-hand gripping rope respectively. Otherwise, both ropes will try to twist the coupling piece in the same rotational direction which would lead to the ropes untwining under load. This would result in a reduction in the breaking force and a structural change in the ropes.
The terminal is a newly constructed and modernised coal terminal which handles the largest coal ships in the world. Usually, hard coal is shipped for the two coal-fired power stations located in Wilhelmshaven and for other power plants in Germany via the wagon loading system. Currently, the annual turnover is around 4 – 5 million tonnes of coal which is steadily increasing due to the acquisition of new customers.
According to Kurt Kühn, head of technology at Rhenus BTW, this steady increase in demand soon resulted in the original rope routing from another rope manufacturer being exchanged for the tried and tested CASAR rope to achieve better service life. In close collaboration with the company Tecklenborg,Kegel GmbH the new CASAR Superplast10 Mix was chosen for its excellent bending exibility and constant wear behaviour over a wide load spectrum.
An initial conclusion can be drawn. On the number 1 level luffing crane, the change from the original rope to the CASAR Superplast10 Mix led to an increase in the handling capacity of almost 14 % per rope set. On the number 2 level luffing crane, the first Superplast10 Mix has not yet reached its discard state. In any case, Mr. Kühn is very satisfied with the rope’s specification.