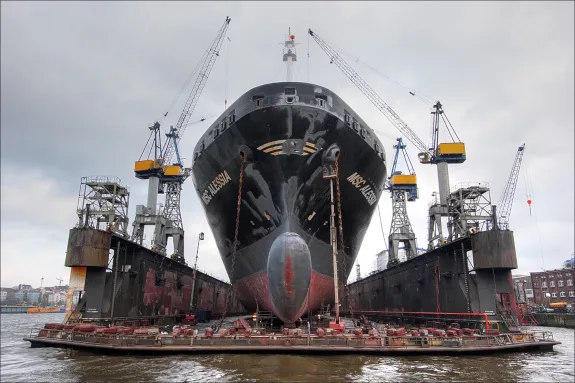
Since 2001, the Danish Odense Steel Shipyard has operated the colossal “Goliath” portal crane. It replaced the shipyard crane blown over by gale-force winds in December 1999.
Now, after 16 years, it is time to replace the ropes in order to ensure continued operation. We are delighted that the German crane manufacturer Takraf Tenova (previously MAN Takraf) continues to have con- "dence in CASAR ropes and has placed an order with us for re-roping the crane. In November 2017, the new ropes were delivered on schedule at Takraf GmbH. The scope of delivery is nearly 14 km of CASAR Turboplast Ø36 mm, half in right hand and left hand ordinary lay respectively. Compared to the original roping from 2001, a higher nominal wire strength and, as a result, a higher minimum breaking force was selected. Otherwise, trust has been placed in the proven CASAR Turboplast Ø 36 mm construction in the galvanised version. The speci"cations and dimensions of the entire crane system are impressive and it is easy to see why the crane was christened “Goliath”: A carrying capacity of 1000 t, a span width of 148 m and lifting height of 114m speak volumes. The crane has 4 trolleys with 6 lifting gears and allows movement of entire ship sections on the spot to the millimetre. Additionally, multiple objects can also be lifted at the same time or objects that are freely suspended can be rotated. In doing so, each of the individual lifting gears can lift up 300 t. The unique method of operation of the crane with multi-layer spooled lifting gears, some of which work with spreaders, imposes high demands on the production tolerances of our ropes. Especially with multi-layer wound drums, even slight deviations with regard to the tolerance constancy of the ropes can lead to tilting of the spreader and gaps in the spooling. Of course, this must also be taken into consideration with single-layer spooling of ropes, but with multi-layer spooling, faults and minor deviations add up with each additional position and as a result, cause a greater negative impact.
The length of the ropes must also be precisely coordinated to prevent tilting. The supplied ropes have a Flemish eye with a solid thimble while the other end is seized. For those who are not familiar with the term “Flemish eye”: In this context, it is a spliced rope loop, which is also secured with a steel ferrule. Such an end connection attains a high level of effectiveness and can withstand high temperatures up to 400°C.
The length of the rope is de"ned from the end of the rope to the centre of the thimble bore. Here the assembly of CASAR can show all its class and experience and bring qualities like dimensional tolerance and expertise to bear in terms of end connections. We wish Odense Steel Shipyard safe and accident-free operations with their “Goliath”.